MUDA
無駄
waste
The whole point of a production process, or indeed any activity which is labeled “work,” is to add value. If so-called “work” doesn’t add value, then it is actually waste. This is the central idea behind the concept of muda.
The formal concept of muda in the industrial context is generally credited to Toyota’s Taiichi Ohno. Like many aspects of the Toyota Production System and “Japanese-style management,” the concern with muda originates in the scarcity of Japan’s postwar years, when Japanese industries always had to do more with less.
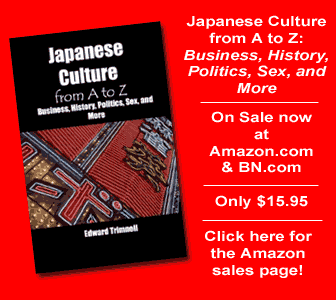
The Seven Categories of Muda
There are seven categories of muda that can exist in the workplace:
-
Overproduction: Producing anything earlier than needed and/or in greater quantities than needed. Overproduction is the “worst type of muda” because it consumes the most company resources: labor, materials, etc.
-
Conveyance: The unnecessary/non-value-added transport of materials and work-in-process between workplace stations. The muda of conveyance is not only wasteful, but it also increases the odds that a product will be damaged before leaving the factory. Conveyance also increases safety risks, as more forklifts, etc. are moving about the workplace.
-
Waiting: Time spent waiting rather than working. If a production worker has to wait for inputs from another process, he or she will be forced to waste the company’s time. Therefore, it is important to align processes correctly.
-
Motion: Any unnecessary movement in a work process. If a worker has to twist and contort himself at a workstation, then much of his effort is in vain. Workstations and processes should be designed so that they can be performed with a minimal amount of stretching, bending, and straining.
-
Rework: Time, effort and materials used to repair defective products. When defective products are created, they sometimes have to be scrapped. Other times, though, it is possible to repair them. This type of defect repair work is commonly called “rework.” Rework never adds value, because it is a repetition of botched work that should have been done correctly in the first place.
-
Over-processing: Processing a workpiece beyond what is necessary. The objective of any production process is to create products to specifications. If a process goes beyond the specifications for a product, then the process is wasteful. For example, if a hole needs to be 5 mm deep, then it is wasteful to drill 7 mm. The extra 2 mm don’t add any value.
-
Inventory: Extra finished products, work-in-process, or supplies. A workplace were excess “stuff” accumulates is a wasteful workplace. The extra “stuff” might be raw materials for production, tools, or maintenance supplies. These extra, unnecessary items take up storage space and increase the company’s cash flow burden.
The identification of muda and its elimination from the workplace are topics that could easily consume an entire book. The above descriptions are therefore necessarily broad.
Finally, I should note that muda is tied to the company’s commitment to conscientious customer service. Any business charges its customers for the work it performs. If a particular aspect of workplace activity does not add value, then the customer wouldn’t want to pay for it—as it doesn’t generate any value.
|